Combination of Sugarcane Bagasse Ash & Waste Glass in Construction
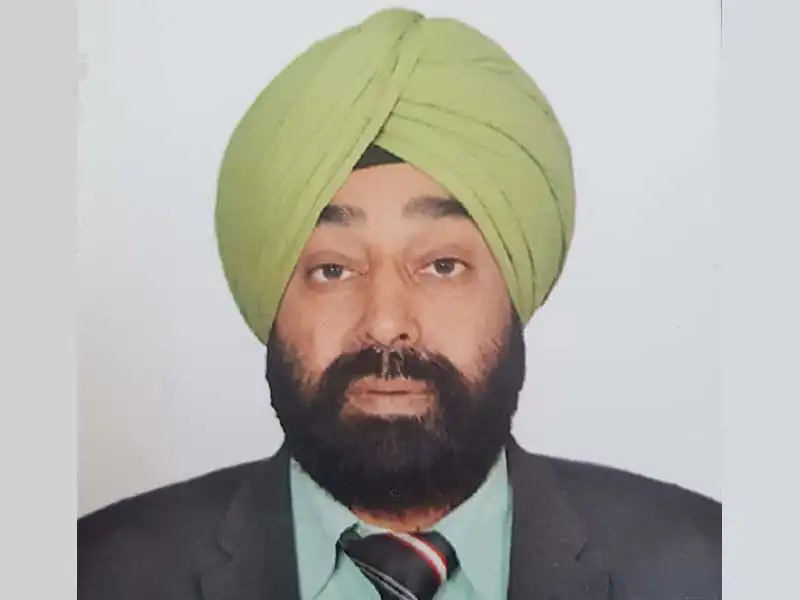
This paper presents an investigation on the effect of Sugarcane Bagasse Ash (SCBA) and Waste Glass (WG) on the workability and compressive strength of concrete. In this study, 25 mixes of concrete were prepared at different replacement levels of SCBA (0 to 20% @ increment of 5%) with cement and WG (0 to 40% @ increment of 10%) with fine aggregates. From results, it can be concluded that the combination of 10% SCBA and 10% WG is most significant for higher strength, cost, and acceptable workability.
The study focuses on the utilization of waste materials in place of concrete ingredients to make concrete industry sustainable and economical. During the production of cement a large amount of CO2 is emitted, which has a very adverse impact on the environment. Extraction of natural aggregates and generation of industrial waste also leads to environmental degradation, ecological imbalance, and environmental pollution. Use of these waste materials not only helps to reduce the use of natural resources but also helps to mitigate environment pollution.
Concrete has become an indispensable part in construction due to its mechanical and durability. Concrete industry is the one of the major consumers of natural resources. The utilization of concrete ingredients such as cement and aggregates has been enhanced, which ultimately results in adverse effects on the environment. Concrete is defined as a composite material obtained by using cement, aggregates and water. Few decades ago, these materials were easily available but nowadays their adverse effect on the environment is in focus. To start with, in Ordinary Portland Cement (OPC), a large amount of green house gas (CO2) is produced from both industrial and fuel combustion. In industrial processes green house gas is emitted due to the heating of limestone (CaCO3) to obtain main oxide (CaO) of OPC. During production of cement fossil fuel, combustion is also responsible for the emission of CO2 by 5%. (Fairbairn et al., 2012). Due to these emissions there is a huge rise in the temperature of the earth, which ultimately give rise to global warming. Moreover, natural sand is another major constituent of concrete as it is used as a fine aggregate. Use of river sand as a fine aggregate leads to the exploitation of river beds, lowering the water table, erosion of land near the river, and damaging structures, which leads to unsustainable development of the nation. It, therefore, becomes very essential and more significant to find substitutes for both cement as well as natural aggregates.
The continuous growth of agro and industrial waste is the cause of many environmental problems which can be reduced by using these wastes in concrete construction.
Food and Agriculture Organization (FAO) states that India is the second largest producer of sugarcane after Brazil. Sugarcane bagasse is a fibrous residue left after extraction of juice from the sugarcane. The sugarcane bagasse consists of 50% cellulose, 25% of hemicelluloses and 25% of lignin. Each ton of sugarcane generates approximately 26% of bagasse and 0.62% of residue ash (Srinivasan and Sathiya, 2010). Most of the bagasse is used as a fuel in boilers, distilleries, and a small amount for power generation in sugar factories. Byproduct of all these processes is sugarcane bagasse ash (SCBA) which is a major industrial waste product. In general, bagasse ash is deposed of in landfills, and is now becoming an environmental burden.
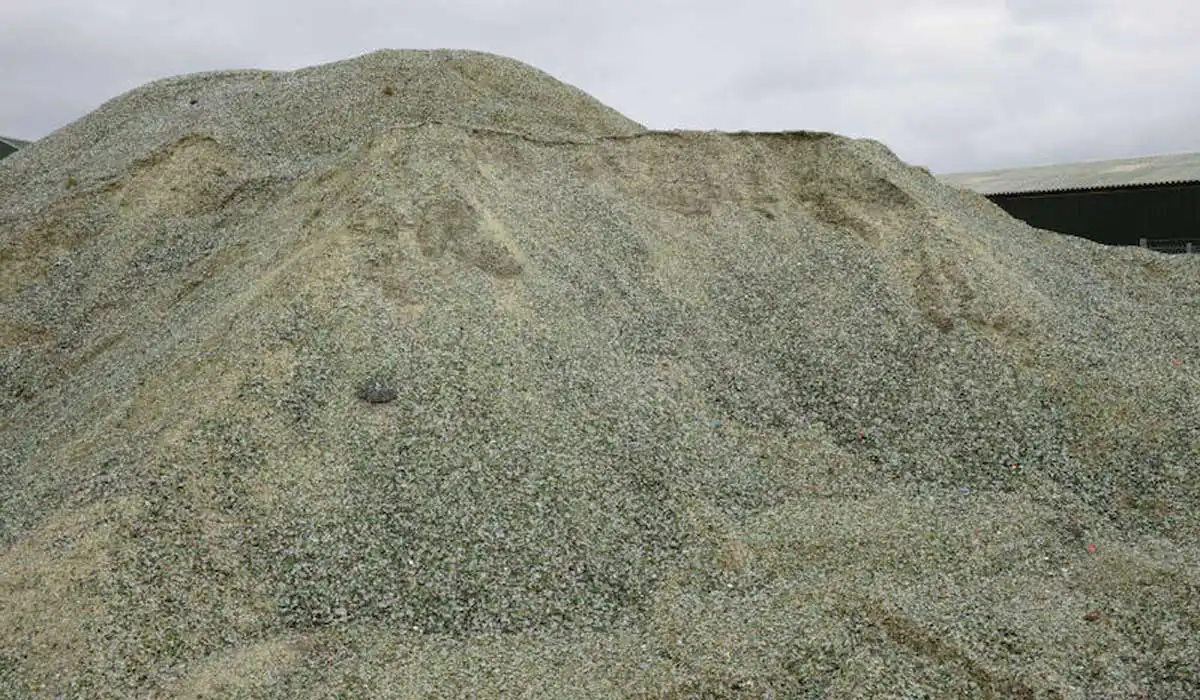
The SCBA results from bagasse combustion mainly consist of silica (SiO2) which indicates its potential as a pozollanic mineral (Chusilp et al., 2009). The use of SCBA as a supplementary cementitious material helps to reduce utilization of cement to a certain extent. Thus, use of bagasse ash not only helps to mitigate the problem of emission of CO2, it also improves the compressive strength of concrete by physical effect (filler effect) as well as chemical effect (pozzolanic effect).
Waste glass is crushed into specified sizes for use as aggregates in various applications such as water filtration, grit plastering, sand cover for sport turf and as sand replacement in concrete. The use of waste glass as a fine aggregate creates a problem in concrete, due to the reaction between alkalis in Portland cement and silica in waste glass, which is called alkali silica reaction (ASR). Due to ASR reaction, silica gel is formed; it absorbs water and volume of gel increases. The swelling of silica gel generates hydrostatic pressure. If this internal pressure exceeds the tensile strength of concrete, cracks will form around concrete structures. But in the use of waste glass as a fine aggregate no reaction was detected. A reaction was detected only when it was used as a coarse aggregate. WG is produced in various forms like container glass (bottles, jars), flat glass (window, windscreens), bulb glass (light globes), cathode ray tube glass (TV screens, monitors) etc. Glass is a unique inert material that can be used in concrete as a partial replacement with cement as well as with aggregates, because it contains large proportion of SiO2 that make it pozzolanic in nature (Shayan, 2002). The utilization of these waste materials with combination provides a satisfactory solution to some of the environment problems associated with waste management. Agro waste like SCBA and domestic as well as industry WG can be used for sustainable development of the concrete industry.
Materials Used Cement
The OPC is basic portland cement and is best suited for use in general concrete construction where there is no exposure to sulphates in the soil or in ground water. In this study, Ordinary Portland Cement (OPC) conformed to BIS: 8112-1989 was used. Compressive strength test, consistency test, setting time test and specific gravity test were conducted to obtain some physical properties of cement. The results of these tests are given in Table 1.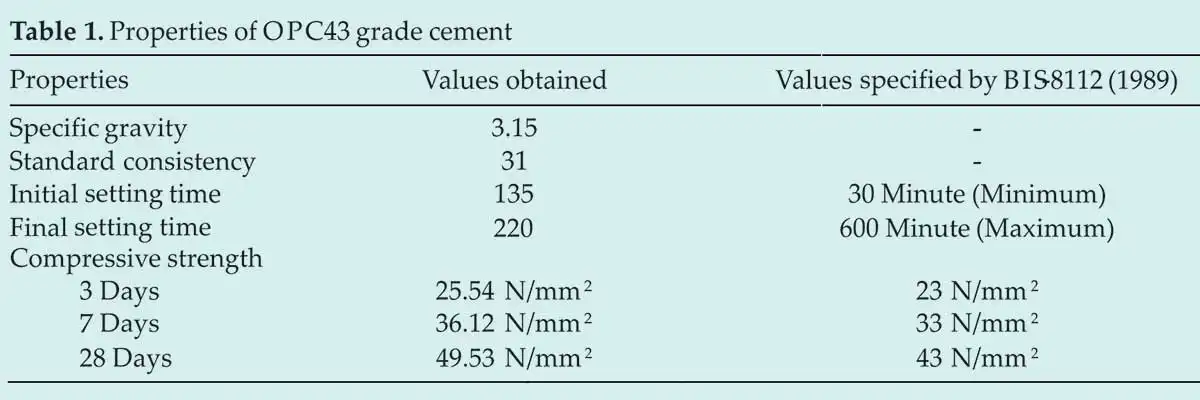
Fine aggregates
An aggregate most of which passes 4.75-mm IS Sieve known as fine aggregates. According to size, the fine aggregates may be classified as coarse, medium, or fine aggregate. Depending upon the particle size distribution, fine aggregates are divided into four grading zones as per BIS-383 (1970) that is, zone I, zone II, zone III and zone IV. In this study fine aggregates confirmed to grading zone II was used. It was brown in color, collected from Chakki River (Pathankot). The specific gravity of fine aggregates was determined as 2.70.Coarse aggregates
Aggregates most of which retained 4.75-mm BIS Sieve are known as coarse aggregates. The graded coarse aggregates are demarcated by their nominal size i.e. 40 mm, 20 mm, 16 mm and 10 mm. Regarding the characteristics of different types of aggregate, crushed aggregates tend to improve the strength because of interlocking of angular particles while rounded aggregates improved the flow because of lower internal friction. Crushed gravel used in present study was collected from Pathankot quarry. Their color was gray. It was a mixture of two stone sizes of 10 mm and 20 mm, with 50-50 proportions. The required properties of aggregates were determined by conducting some tests, conforming to BIS-383 (1970). Specific gravity of coarse aggregates was determined as 2.65.Water
Fresh and clean tap water was used for casting the specimens in the present study. The water was relatively free from organic matter, silt, oil, sugar and acidic material as per BIS-456 (2000).Sugarcane bagasse ash
Sugarcane bagasse ash is produced when bagasse is reutilized as a biomass fuel in boilers for vapor and power generation in sugar mills. When this bagasse is burned under controlled temperature, it results into ash. Bagasse ash was collected from the boiler of a sugar mill situated at village Budhewal which falls at a distance of about 4 kms from Jandaili on Ludhiana-Chandigarh road. The collection of the ash was carried out during the boiler cleaning operation throughout three months. The chemical properties of SCBA are given in Table 2.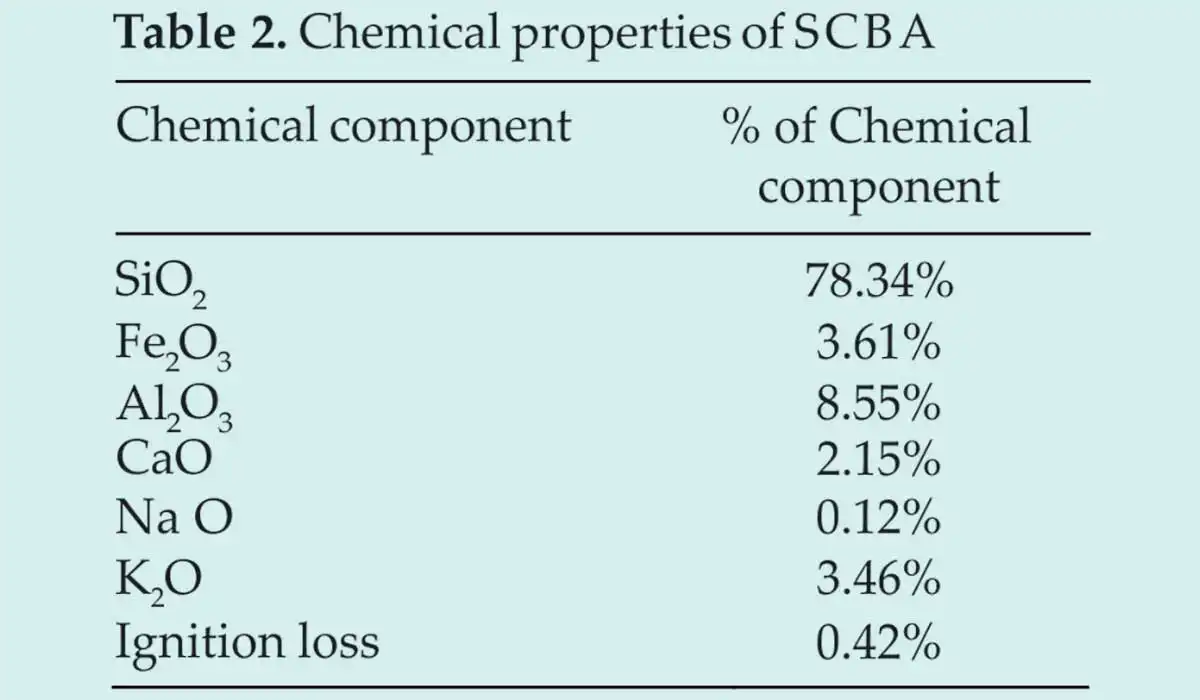
Waste glass
Waste glass is produced in various forms like container glass (bottles, jars), flat glass (window, windscreens), bulb glass (light globes), cathode ray tube glass (TV screens, monitors) etc was collected.It was pulverized in los angles abrasion apparatus. There, after sieved through 4.75-mm Sieve. The specific gravity of waste glass was 2.45.
Laboratory Testing Program
Mix design and sample preparation
Twenty five concrete mixes were prepared each with 0.55 water/cement ratio. First mix was designated as control mix (S1) designed as per BIS-10262 (2009). Then remaining mixes were prepared by replacing cement with SCBA (0 to 20% @ increment of 5%) and fine aggregates with Waste Glass (0 to 40% @ increment of 10%). Water content, cement content and coarse aggregates were constant in all mixes. In this study, cubes of sizes 150mm were casted. The mix proportions selected for this study are given in Table 3.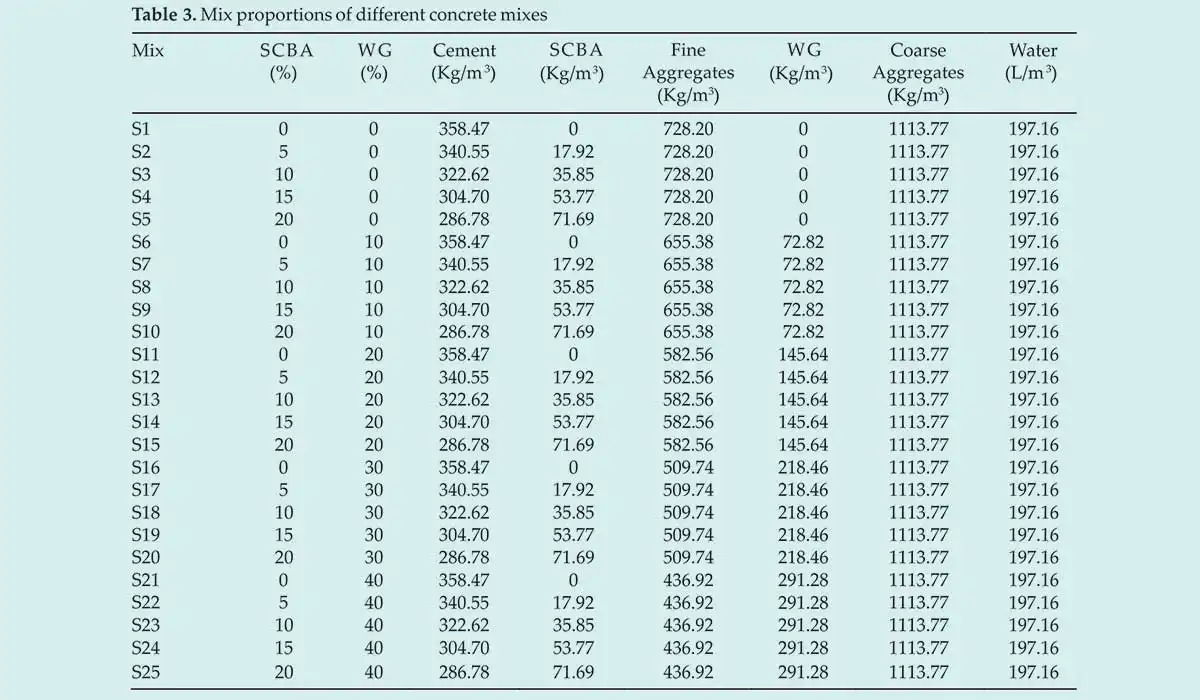
Workability of concrete
Workability is that property of freshly mixed concrete or mortar which determines the ease and homogeneity with which it can be mixed, placed, consolidated, and finished. Workability is not just based on the properties of the concrete but also on the nature of the application. In present study, workability of each mix was measured in terms of slump.Compressive strength of concrete
In determining the effect of addition of SCBA and Waste Glass on compressive strength of concrete, a compression test was done by subjecting cube under digital Universal Testing Machine (UTM) of 9000kN capacity as per BIS-516 (1959). The samples were cured under water for a period of 14, 28 and 60 days.Results and Discussion
Workability
Slump test apparatus was used to determine the workability of concrete, immediately after preparing fresh concrete. The slump values of each mixture are given in Table 4 and presented in Fig 1.
From the above results, we can conclude that the workability of concrete decreased with increase in percentage of SCBA, while there is a huge incline in workability with increase in percentage of waste glass. The slump value falls down from 110 to 91 with 0% to 40% replacement of SCBA with cement, due to rough and angular shape of SCBA partials. It was observed that the slum value was highest at 0% replacement of SCBA with combination of 40% waste glass (WG) about 133. This is mainly due to the non porous structure of the waste glass.
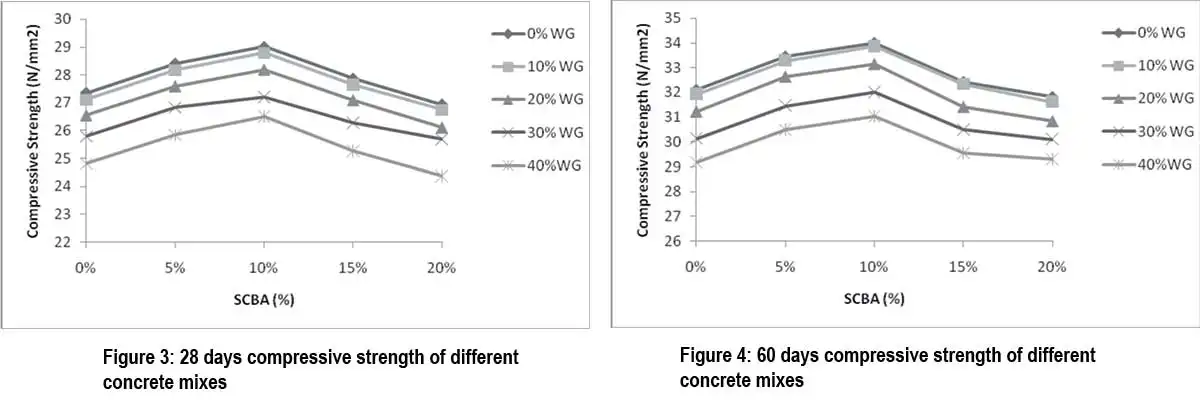
Compressive Strength
The compressive strength of all the mixes was determined at the ages of 14, 28 and 60 days for the various replacement levels of SCBA with cement and WG with fine aggregates. The values of average compressive strength and percentage loss for different replacement levels of SCBA (0%, 5%, 10%, 15%, and 20%) and WG (0%, 10%, 20%, 30% and 40%) at the end of different curing periods (14 days, 28 days & 60 days) are given in Table 5. The effect of both waste materials on compressive strength at curing ages of 14, 28 and 60 days is illustrated in Figure 2, 3 and 4 respectively. It is quite obvious from the data that there was a gradual incline in compressive strength as the percentage of SCBA is increased up to 15%. After 15%, the value of compressive strength suddenly falls down at all curing periods. The highest percentage gain was observed at 10% SCBA replacement level about 4.6, 6.1 and 5.9 at 14, 28 and 60 days curing respectively. Nevertheless, the replacement of 15% of SCBA still improves the compressive strength of concrete as compared to the control concrete but for much better results, the 10% of SCBA seems to be the optimum. This improvement is basically due to physical as well as chemical effect of SCBA. SCBA is pozzolanic in nature due to the presence of silica content, which affected the chemical reaction between relative silica and calcium hydroxide. The filler effect (physical effect) also enhances the strength of concrete. In contrast, there was a loss in strength of concrete due to replacement of fine aggregates with WG. The substitution of WG produced relatively low strength concrete compared to control mix. This decline may be due to the decrease in adhesive strength between the surface of the waste glass aggregates and the cement paste as well as the increase in fineness modulus (FM) of the fine aggregates and the decrease in compacting factor in accordance with the increase in the mixing ratio of the waste glasses. At the curing age of 14 days, there was about 0.6%, 2.5%, 5.9% and 8.1% loss in compressive strength of concrete containing 10%, 20%, 30%, and 40% WG as fine aggregates respectively. The same trend was observed for curing period of 28 and 60 days. It can be seen that the loss in compressive strength was minor up to 10% of WG but beyond 10%, there was large reduction in compressive strength. From Table 5, it can be concluded that the combination of 10% SCBA and 20% WG give better results without any loss in strength. While to make higher strength concrete compared to reference mix, the combination of 10% SCBA and 10% WG is the most significant.Cost analysis
Cost analysis of concrete can be done by multiplying the cost of concrete ingredients with their respective quantity. However, the cost of concrete ingredients depends upon the transportation charges as well as manufacturing charges. While, it is not relevant to include transportation charges because transportation price depends on the distance between manufacturing place and delivery destination. Thus, in present research the cost analysis of concrete has been done without considering the transportation expenditure (Table 6 to Table 8).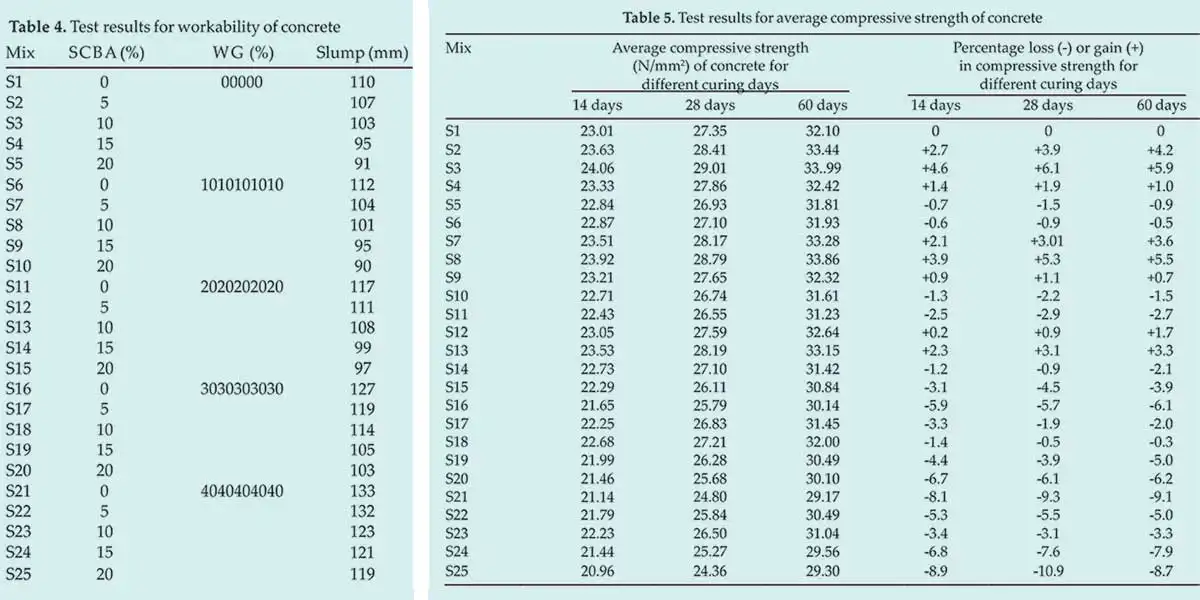
The present results depicts that the cost of concrete decreases as percentage of SCBA increases while the replacement of WG is unable to make changes in the cost of concrete. The cost of concrete remains same as the reference mix at every replacement level. In mixes S5, S10, S15, S20, and S25, about 11.3% reduction is observed while at the same time strength of concrete also decreases. Moreover, mix S8 and S13 reduces 5.7 percent cost of concrete which is recommended for higher strength and acceptable workability. Therefore, this analysis spreads the awareness towards the use of these waste materials in concrete which provides economic benefits for concrete industries.
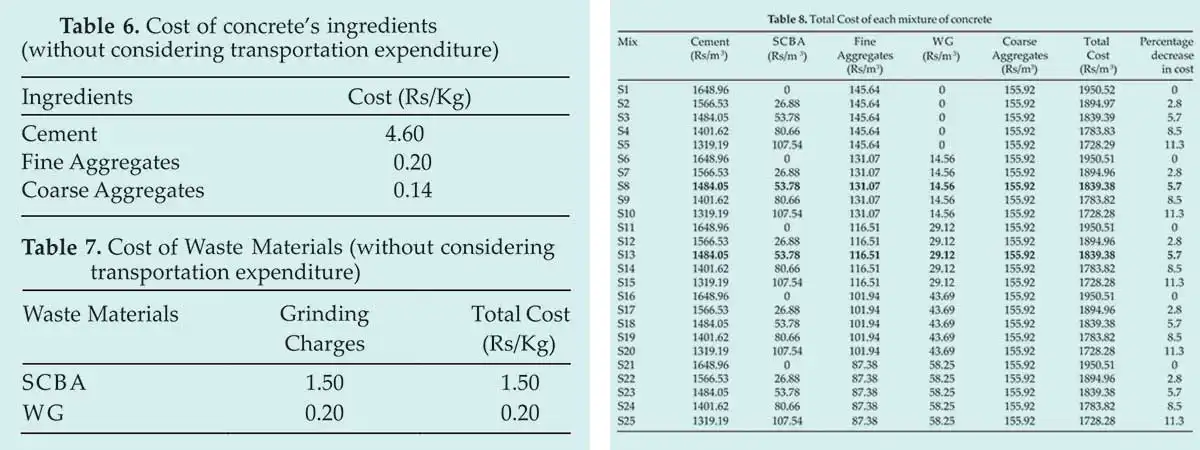
Conclusions
From all data given in Tables and plotted in Figures, it can be concluded that:- The workability of concrete decreases with the increase in SCBA content while increases with the increase in WG content.
- The slump values decreased from 110 mm to 90 mm, when the percentage of SCBA is increased from 0% to 20%. However, as the percentage of WG is increased from 0% to 40% workability starts increasing from 110 mm to 135 mm.
- The compressive strength of concrete increases as SCBA content increases for all curing ages. The maximum improvement in compressive strength is observed at 10% of SCBA but beyond 10% replacement of SCBA strength starts decreasing. There is a significant reduction in compressive strength at 20% replacement of SCBA.
- The replacement of WG with fine aggregates decreases the compressive strength of concrete for all curing ages. As the percentage of WG increases there is a continuous loss in strength at every replacement level.
- The combination of 10% SCBA and 20% WG give better results without any loss in strength. While to make higher strength concrete compared to reference mix, the combination of 10% SCBA and 10% WG is most significant for higher strength and acceptable workability.
- The cost analysis shows that the utilization of waste materials is not only eco-friendly solution but also provides economic benefits to concrete industries.
ICCT - September - October 2023