Developing a CO2- Neutral Cement & Concrete Industry
The cement and concrete industry are bringing innovative solutions and are adapting the latest processes and ingredients to shift towards greater sustainability. By adopting the right analytical strategy cement producers can bring carbon neutral cement within reach of the construction industry.
Malvern Panalytical
Manufacturing cement has always been a highly technical process requiring tight control of each production step. Now, the need to drive a more sustainable industry presents additional challenges. Manufacturers aim to conserve natural resources while lowering energy consumption and greenhouse gas (GHG) emissions – all without affecting profitability. Indeed, many companies have committed to reducing their CO2 emissions by 30% by 2030 compared with 1990 and are expecting to achieve lifetime neutrality for concrete by 2050.
Achieving these goals requires continuous adjustments across the whole value chain - from raw materials to final product. Several new solutions to reduce CO2 emissions in cement production are now being explored – in particular, cutting clinker emissions and creating ‘green’ cements. As well as supporting sustainability and circularity targets, these approaches can also deliver cost reductions.
Image 1: Inert cement rotary kiln machine at night
Process efficiency, energy consumption, emissions, and final product quality are all key parameters here, and are affected by a range of factors. The raw materials’ elemental and mineralogical composition and fineness, the intermediates and additives added, and the quality of any alternative fuels all have an impact on outcomes. As such, high-quality materials characterization – particularly automated solutions – is more important than ever in making these new solutions successful.
Cement manufacturers can adjust particle size distribution using lab-based or in-field particle size analyzers, and monitor crystalline phases using X-ray diffraction (XRD). When implemented as part of automated control of the finishing circuit, these solutions enable higher throughputs, reduced energy consumption, and effective use of replacement materials – in turn, this delivers both cost and CO2 reductions.
Another impactful way to optimize is to maintain stable chemical composition in the raw meal, which helps to ensure consistent heat profiles in the kiln. Controlling the kiln’s oxidizing conditions is also essential for preventing both grindability issues and powder formation when Beta-C2S belite converts to Gamma-C2S. X-ray fluorescence (XRF), X-ray diffraction (XRD), neutron analyzers, and particle size analyzers all offer accurate, rapid control of these parameters and help to optimize energy-efficiency in clinker production.
Image 2: Shredded municipal waste in front of rotary cement kiln used as alternative fuel
These characterizations can be carried out using XRF for chemical and elemental composition (including heavy metals), XRD for crystallography, amorphous composition, oxidated or reduced forms, and laser diffraction for particle size analysis to optimize combustion and circulation in the kiln.
Image 3: CNA Cross-belt analyzer from Malvern Panalytical
One way to reduce these carbon dioxide emissions is to supplement the limestone with materials such as blast-furnace slag from steel production, fly-ash from coal power plants, silica fume, calcined clays, pozzolans, and other industrial waste. Not only does this keep these by-products out of landfill, it also means less clinker is needed, cutting emissions by as much as half.
Enhanced recent blended cement combining limestone with calcined (dehydroxylated) clay to partially replace clinker is a particularly promising solution. The resulting limestone calcined clay cement (LC3) can enable CO2 emission reductions of up to 30-40% compared with OPC, and the calcined clay and limestone promote early hydration. Because clinker and the ratio of calcined clay to limestone both affect the cement’s compressive strength, characterizing their properties is important. This can be done using loss on ignition (LOI), XRF, and XRD.
Alternative green cementitious materials can also be made using geopolymers or calcium sulphoaluminate, which can be a ye’elimite-based system or a belite-based system. The former can replace OPC at a ratio of 1:2, and the latter can be used as a 100% replacement of OPC. CSA clinker is much softer than OPC clinker and can be calcinated at 1250° C, rather than OPC’s 1450° C – saving around 30% in CO2 and 15-20% in fuel and grinding energy. In addition, this special cement distinguishes itself from Portland cement through high-speed bonding, fast strength development, and shrinkage reduction.
So, it’s certainly possible to achieve both CO2 reduction and profit improvements, and materials analysis remains essential both to manage these processes and ensure a high-quality final product.
Through good sampling, regular control checks, and timely feedback, automation can enable maximum product performance and better, cheaper cement – both classical and green. Large, accurate datasets from multiple analyzers and sensors are crucial for futureproof clinker and cement production.
The consistent and reliable data provided by these next-generation instruments can help reduce production costs by controlling the chemical composition of raw materials, optimizing fuels and power costs, and helping to meet quality requirements. Controlling production through automated, on-line analysis also reduces human error and minimizes non-conformities.
On-line solutions, such as the CNA cross-belt and Insitec particle size analyser, are particularly useful in busy industrial production environments as they address the very common sampling representativity issue that is one of the most critical steps in the monitoring and control process.
As an industry, cement and concrete has a natural advantage – materials analysis has always been an integral part of our processes. Implementing a connected, futureproof analytical strategy is the natural next step. In combination with more efficient manufacturing practices, higher recycling rates, electrification, hydrogen, renewable power, and carbon capture, industrial emissions could be cut by about three-quarters by 2050. While these solutions come with a cost, they also enable significant cost savings for cement manufacturers. This is how profit and planet can go hand-in-hand.
Malvern Panalytical
Manufacturing cement has always been a highly technical process requiring tight control of each production step. Now, the need to drive a more sustainable industry presents additional challenges. Manufacturers aim to conserve natural resources while lowering energy consumption and greenhouse gas (GHG) emissions – all without affecting profitability. Indeed, many companies have committed to reducing their CO2 emissions by 30% by 2030 compared with 1990 and are expecting to achieve lifetime neutrality for concrete by 2050.
Achieving these goals requires continuous adjustments across the whole value chain - from raw materials to final product. Several new solutions to reduce CO2 emissions in cement production are now being explored – in particular, cutting clinker emissions and creating ‘green’ cements. As well as supporting sustainability and circularity targets, these approaches can also deliver cost reductions.
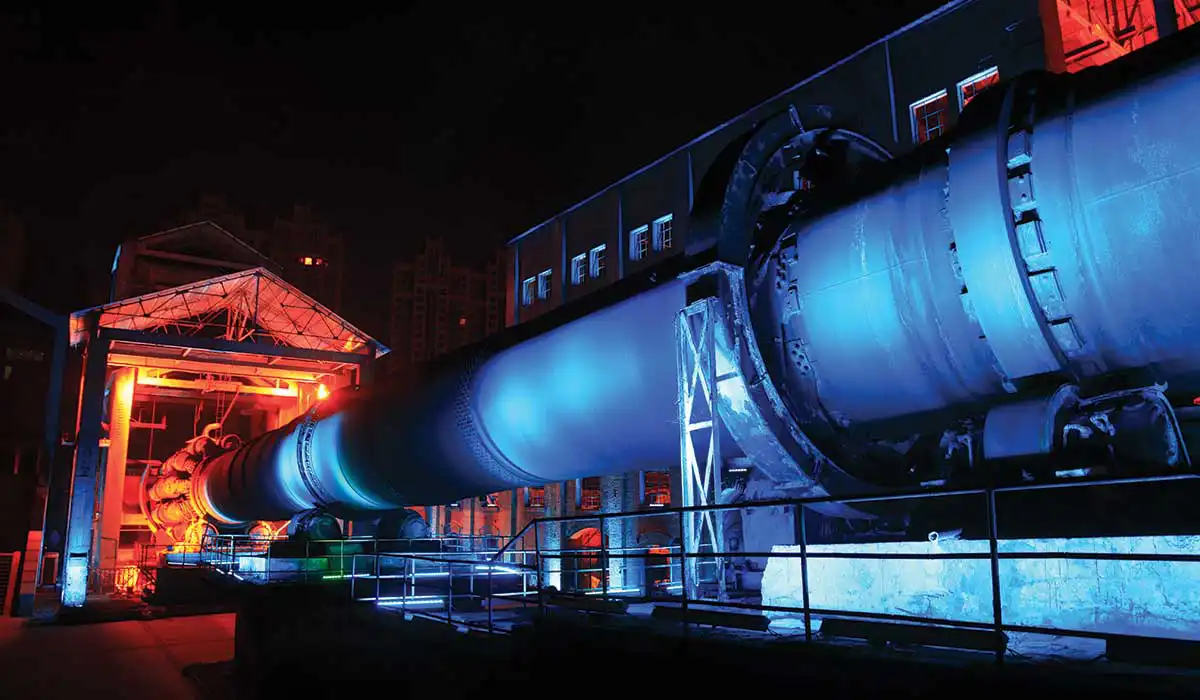
Process efficiency, energy consumption, emissions, and final product quality are all key parameters here, and are affected by a range of factors. The raw materials’ elemental and mineralogical composition and fineness, the intermediates and additives added, and the quality of any alternative fuels all have an impact on outcomes. As such, high-quality materials characterization – particularly automated solutions – is more important than ever in making these new solutions successful.
Improving process and kiln efficiency
Optimizing operating conditions in the raw milling and pyro-processing stages play a big role in ensuring maximum efficiency. Firstly, it’s key to raw mix particles to be fine enough, as coarse calcite or quartz grains or silica particles lead to large clusters of alite and belite, making the clinker difficult to grind and diminishing strength.Cement manufacturers can adjust particle size distribution using lab-based or in-field particle size analyzers, and monitor crystalline phases using X-ray diffraction (XRD). When implemented as part of automated control of the finishing circuit, these solutions enable higher throughputs, reduced energy consumption, and effective use of replacement materials – in turn, this delivers both cost and CO2 reductions.
Another impactful way to optimize is to maintain stable chemical composition in the raw meal, which helps to ensure consistent heat profiles in the kiln. Controlling the kiln’s oxidizing conditions is also essential for preventing both grindability issues and powder formation when Beta-C2S belite converts to Gamma-C2S. X-ray fluorescence (XRF), X-ray diffraction (XRD), neutron analyzers, and particle size analyzers all offer accurate, rapid control of these parameters and help to optimize energy-efficiency in clinker production.
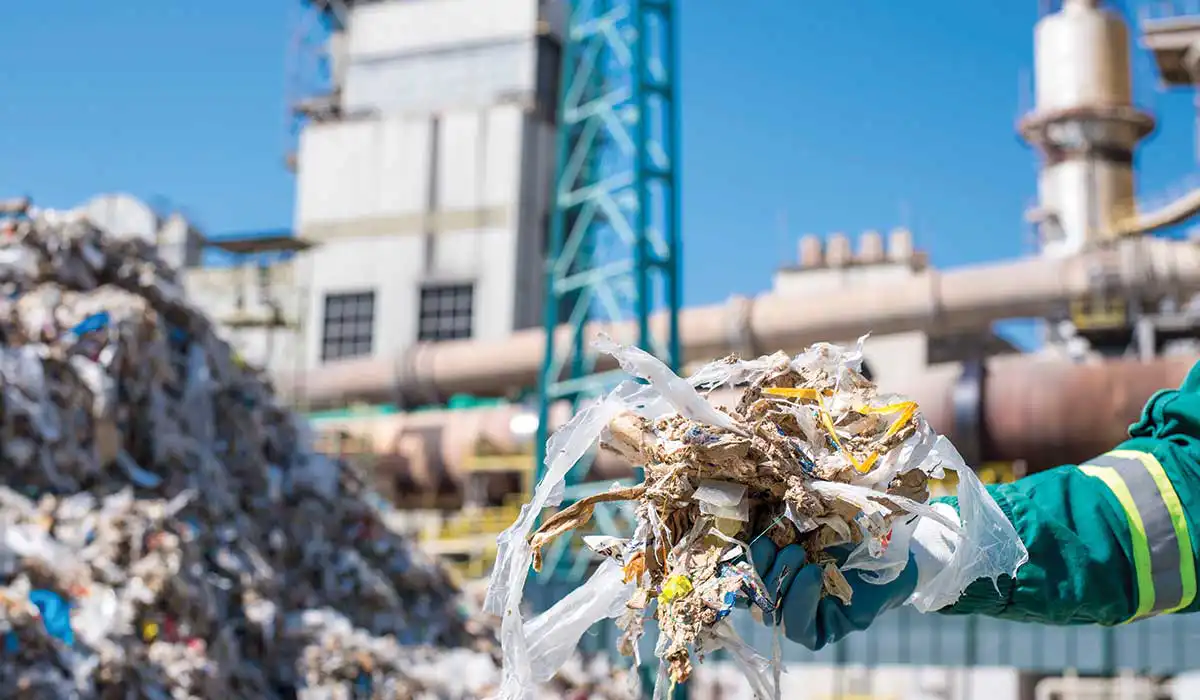
Using alternative fuels
Waste management solutions such as pre-processing and co-processing can help reduce environmental impact by enabling improved resource efficiency. Co-processing involves reducing direct CO2 emissions using alternative fuels that recover the calorific value of waste, such as:- Biomass fuels, such as rice husk and sewage sludge;
- Mixed fuels, such as used tires or refuse-derived fuels from municipal solid waste;
- Fossil-waste fuels with lower emissions factors.
- Avoiding CO2 emissions from open burning or incineration without energy recovery;
- Avoiding methane emissions from dumpsites and landfills without landfill gas capture.
These characterizations can be carried out using XRF for chemical and elemental composition (including heavy metals), XRD for crystallography, amorphous composition, oxidated or reduced forms, and laser diffraction for particle size analysis to optimize combustion and circulation in the kiln.
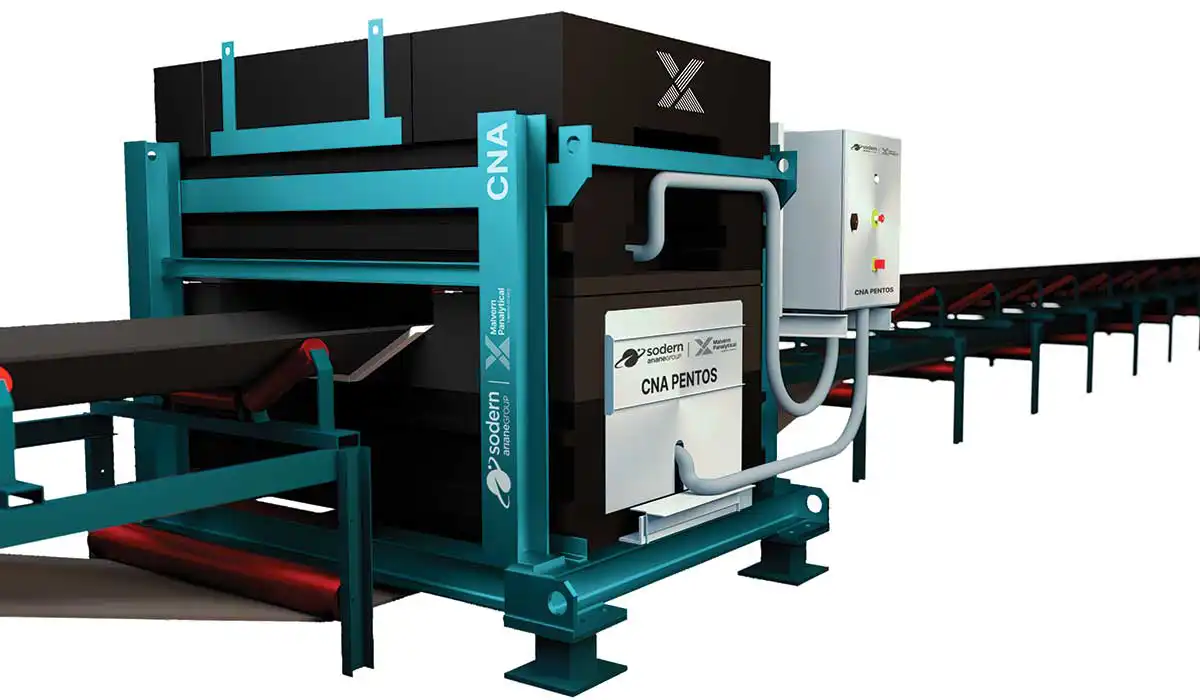
Alternative materials for ‘green’ cements
Over 85% of the cement industry’s emissions are generated during clinker production. Improved production efficiency helps, but 60% of emissions within that 85% come from inevitable chemical reactions from heating limestone. For every molecule of limestone that is used to make Portland cement (OPC), a molecule of carbon dioxide is released.One way to reduce these carbon dioxide emissions is to supplement the limestone with materials such as blast-furnace slag from steel production, fly-ash from coal power plants, silica fume, calcined clays, pozzolans, and other industrial waste. Not only does this keep these by-products out of landfill, it also means less clinker is needed, cutting emissions by as much as half.
Enhanced recent blended cement combining limestone with calcined (dehydroxylated) clay to partially replace clinker is a particularly promising solution. The resulting limestone calcined clay cement (LC3) can enable CO2 emission reductions of up to 30-40% compared with OPC, and the calcined clay and limestone promote early hydration. Because clinker and the ratio of calcined clay to limestone both affect the cement’s compressive strength, characterizing their properties is important. This can be done using loss on ignition (LOI), XRF, and XRD.
Alternative green cementitious materials can also be made using geopolymers or calcium sulphoaluminate, which can be a ye’elimite-based system or a belite-based system. The former can replace OPC at a ratio of 1:2, and the latter can be used as a 100% replacement of OPC. CSA clinker is much softer than OPC clinker and can be calcinated at 1250° C, rather than OPC’s 1450° C – saving around 30% in CO2 and 15-20% in fuel and grinding energy. In addition, this special cement distinguishes itself from Portland cement through high-speed bonding, fast strength development, and shrinkage reduction.
So, it’s certainly possible to achieve both CO2 reduction and profit improvements, and materials analysis remains essential both to manage these processes and ensure a high-quality final product.
Automation: even better monitoring and efficiency
For maximum cost-efficiency, an automated approach is becoming increasingly important. Solutions range from individual instruments that can automate a single routine process through to on-line real-time analysis and full-scale automated laboratories.Through good sampling, regular control checks, and timely feedback, automation can enable maximum product performance and better, cheaper cement – both classical and green. Large, accurate datasets from multiple analyzers and sensors are crucial for futureproof clinker and cement production.
The consistent and reliable data provided by these next-generation instruments can help reduce production costs by controlling the chemical composition of raw materials, optimizing fuels and power costs, and helping to meet quality requirements. Controlling production through automated, on-line analysis also reduces human error and minimizes non-conformities.
On-line solutions, such as the CNA cross-belt and Insitec particle size analyser, are particularly useful in busy industrial production environments as they address the very common sampling representativity issue that is one of the most critical steps in the monitoring and control process.
Way forward
Developing a CO2-neutral cement and concrete sector is certainly a daunting challenge – but the industry and its partners are bringing a wide range of innovative solutions to this task. By adapting both processes and ingredients successfully, the sector has the opportunity to lead by example as part of the wider shift toward greater sustainability.As an industry, cement and concrete has a natural advantage – materials analysis has always been an integral part of our processes. Implementing a connected, futureproof analytical strategy is the natural next step. In combination with more efficient manufacturing practices, higher recycling rates, electrification, hydrogen, renewable power, and carbon capture, industrial emissions could be cut by about three-quarters by 2050. While these solutions come with a cost, they also enable significant cost savings for cement manufacturers. This is how profit and planet can go hand-in-hand.
ICCT - September - October 2023