Geopolymer Building Blocks for Sustainable Masonry Construction
Radhakrishna, Professor and Head, Department of Civil Engineering, RV College of Engineering, Affiliated to Visvesvaraya Technological University, Bengaluru and G S Manjaunath, Professor, Department of Civil Engineering, Gogte Institute of Technology, Affiliated to Visvesvaraya Technological University, Belagavi.
Geopolymer building blocks are a sustainable alternative to conventional bricks. Made from fly ash and cured at room temperature, these blocks offer similar strength and density to bricks but with lower water absorption. Geopolymer building blocks appear to be a promising alternative.
Geopolymers belong to a category of non-conventional and non-Portland cement based cementitious binders and they are produced using industrial byproducts like fly ash and ground granulated blast furnace slag (GGBS). This paper reports the development of geopolymer mortars for production of masonry units. The geopolymer mortars were prepared by mixing the mentioned byproducts with manufactured sand and a liquid mixture of sodium silicate and sodium hydroxide solutions. After curing at ambient conditions (by storing in open air), the masonry units were tested for strength properties such as compression, bond-shear, and stress-strain behavior, besides durability related properties such as resistance to aggressive chemicals, elevated temperature and alternate wet and dry cycles. The performance of geopolymer blocks were found to be superior to conventional burnt clay bricks/cement blocks and they were used in construction of a small prototype building. Though in the present work, the geopolymer was found to loose significant strength (up to about 40%) on exposure to 4 hours of 800oC, exploratory studies show by proper selection and proportioning of ingredients of geopolymer mix, this strength loss can be eliminated, even, there is possibility of noticeable strength gain.
The history of masonry construction is regarded as the beginning of civil engineering. Masonry is one of the oldest methods of construction which has been built for the aesthetics and durability. Masonry is building structure with individual units called as masonry units; it is well bonded by mortar between units. In the 19th century, Park Guell in Barcelona, a famous monument was built using reinforced masonry designed by Spanish architect Antoni Gaudi [1]. In the present construction masonry has been widely used in the construction of the residential buildings, commercial buildings and public buildings. Masonry structures would perform variety of functions like, supporting loads, dividing and subdividing the space, provide aesthetic appearance, thermal and acoustic insulations etc. The traditional types of masonry units are burnt clay bricks, hollow blocks, solid blocks and stabilized mud blocks. These masonry units are adopted based on requirements like, compressive strength, accessibility, cost and ease of construction. The masonry mortar is used to bond the masonry units together. In India, there are about 1lakh brick manufacturing industries producing 140 billion bricks per year. It consumes around 400 million tonnes of top fertile soil. Also nearly 25 million tonnes coal and fossil fuel is required for burning of bricks and it is energy intensive material [3]. Brick industries are releasing annually 28% of sulphur oxide to the atmosphere which is one of the major air pollutant.Cement which is the main ingredient in the manufacture of cement concrete blocks. produces considerable amount of carbon dioxide. It contributes nearly 7% of world’s emission which leads into global warming [4].
Thus, manufacturing of burnt clay brick and cement leads to hazardous to environment. Hence there is need to develop alternative masonry units, one of which can be geopolymer unit. Geopolymers are the family of binders formed by using alkaline solutions and alumino silicates like fly ash, metakolin, Ground granulated blast furnace slag (GGBS), resulting in three dimensional aluminosilicate polymeric gel. Geopolymers are environmental friendly as they makes use of industrial by-products and eliminates the use of conventional cement.
Geopolymer is the term coined by Professor Joseph Davidovits for the family of high alkali binders formed in a reaction called as geopolymerization [5]. Many researchers have reported that the utilization refractory concrete can be made using quartz sand, alumina powder, zeolites and rice husk using geopolymer [6-7].
The use of fly ash and GGBFS in concrete can result in achieving considerable compressive and split tensile, bond strength [8-14]. Different geopolymer composites can be made using geopolymers and phenomenological models can be developed to re-proportion them [15-20]. Many researchers have used manufactured sand and recycled water to develop geopolymer concrete and masonry units [21-30]. The use of 5-10% paper sludge by replacement of fine aggregates in fresh concrete can increase the compressive and tensile strength of geopolymer concrete [31-32].The reported literature is scant about the properties and applications of geopolymer masonry units. This research addresses these issues.
The fly ash, GGBSF and M-sand were first mixed thoroughly in dry condition and then alkali solution was added to prepare fresh mortar. The geopolymer block/bricks were prepared by compressing the required amount of mortar. The geopolymer bricks/blocks were cured in open air. The masonry units were tested for water absorption, initial rate of water absorption and density. The compressive and shear bond strengths were also determined along with modulus of elasticity.
The variation of compressive strength of the units with age is indicated in Fig. 1. It can be observed that the compressive strength of the masonry units at the age of 24 hours is more than 5 MPa. This would be sufficient to handle the units for various purposes. The strength increases with age ranging from 5-32 MPa for the units.
The flexural and shear bond strength of the masonry units are very important properties. These propertiwes are shown in Table 5. It was found that flexural strength was more than 2 MPa nd shear bond strength is more than 0.5 MPa which is comparatively better than the traditional masonry.
The variation of stress and strain was found be similar as that of traditional masonry unit as indicated in Fig.2 .The modulus of elasticity of geopolymer masonry block was found to be 9700MPa at the age of 28 days.
Figure 5.25: Variation of residual compressive strength with duration of exposure under sulphate and acid attack.
Geopolymer building blocks are a sustainable alternative to conventional bricks. Made from fly ash and cured at room temperature, these blocks offer similar strength and density to bricks but with lower water absorption. Geopolymer building blocks appear to be a promising alternative.
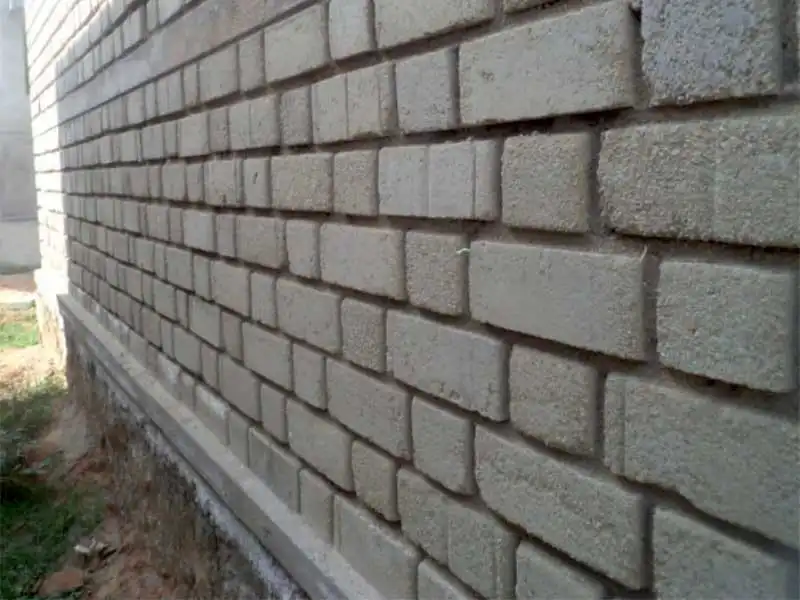
The history of masonry construction is regarded as the beginning of civil engineering. Masonry is one of the oldest methods of construction which has been built for the aesthetics and durability. Masonry is building structure with individual units called as masonry units; it is well bonded by mortar between units. In the 19th century, Park Guell in Barcelona, a famous monument was built using reinforced masonry designed by Spanish architect Antoni Gaudi [1]. In the present construction masonry has been widely used in the construction of the residential buildings, commercial buildings and public buildings. Masonry structures would perform variety of functions like, supporting loads, dividing and subdividing the space, provide aesthetic appearance, thermal and acoustic insulations etc. The traditional types of masonry units are burnt clay bricks, hollow blocks, solid blocks and stabilized mud blocks. These masonry units are adopted based on requirements like, compressive strength, accessibility, cost and ease of construction. The masonry mortar is used to bond the masonry units together. In India, there are about 1lakh brick manufacturing industries producing 140 billion bricks per year. It consumes around 400 million tonnes of top fertile soil. Also nearly 25 million tonnes coal and fossil fuel is required for burning of bricks and it is energy intensive material [3]. Brick industries are releasing annually 28% of sulphur oxide to the atmosphere which is one of the major air pollutant.Cement which is the main ingredient in the manufacture of cement concrete blocks. produces considerable amount of carbon dioxide. It contributes nearly 7% of world’s emission which leads into global warming [4].
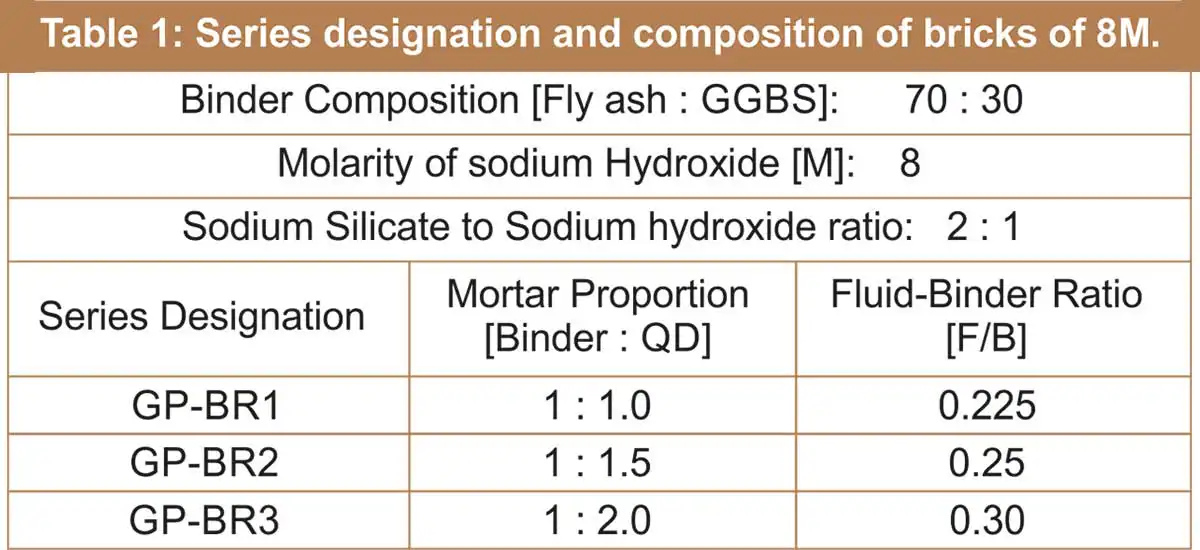
Thus, manufacturing of burnt clay brick and cement leads to hazardous to environment. Hence there is need to develop alternative masonry units, one of which can be geopolymer unit. Geopolymers are the family of binders formed by using alkaline solutions and alumino silicates like fly ash, metakolin, Ground granulated blast furnace slag (GGBS), resulting in three dimensional aluminosilicate polymeric gel. Geopolymers are environmental friendly as they makes use of industrial by-products and eliminates the use of conventional cement.
Geopolymer is the term coined by Professor Joseph Davidovits for the family of high alkali binders formed in a reaction called as geopolymerization [5]. Many researchers have reported that the utilization refractory concrete can be made using quartz sand, alumina powder, zeolites and rice husk using geopolymer [6-7].
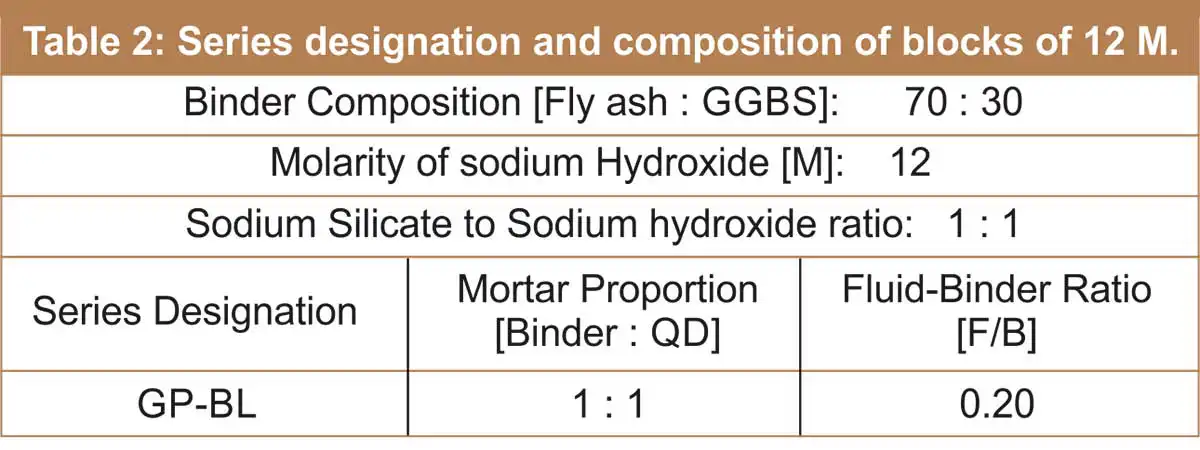
The use of fly ash and GGBFS in concrete can result in achieving considerable compressive and split tensile, bond strength [8-14]. Different geopolymer composites can be made using geopolymers and phenomenological models can be developed to re-proportion them [15-20]. Many researchers have used manufactured sand and recycled water to develop geopolymer concrete and masonry units [21-30]. The use of 5-10% paper sludge by replacement of fine aggregates in fresh concrete can increase the compressive and tensile strength of geopolymer concrete [31-32].The reported literature is scant about the properties and applications of geopolymer masonry units. This research addresses these issues.
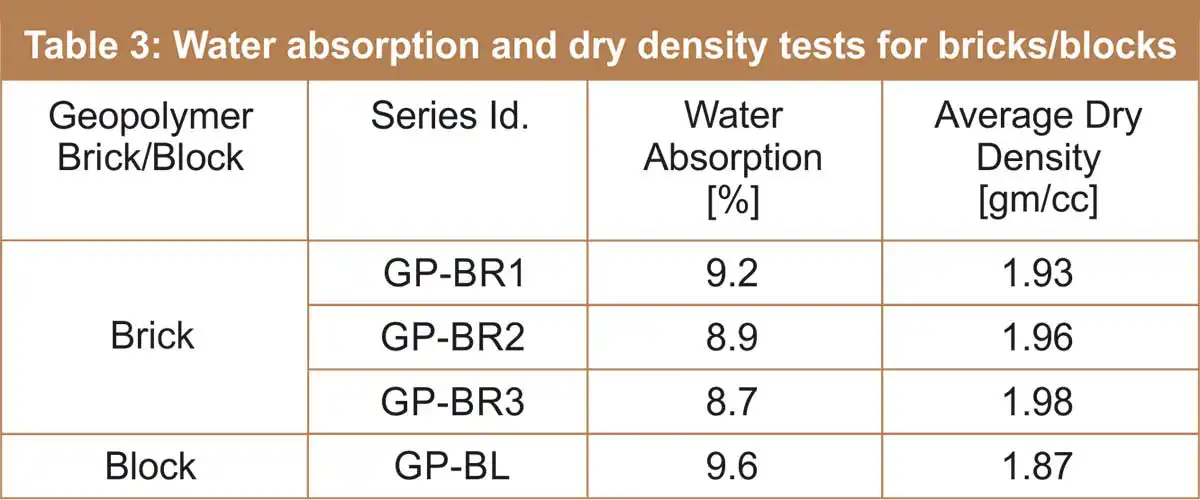
Research Significance
The development of geopolymer masonry units is a relatively new concept, whereas, the research on geopolymer concrete is extensively reported. In case of geopolymer concrete, the use of alkaline salts is considerably high which may not be economically feasible always. The amount of alkaline salts can be considerably reduced in making these masonry units. Determination of strength and durability of these units will boost the confidence level of the field engineer. Thus the present study will be useful.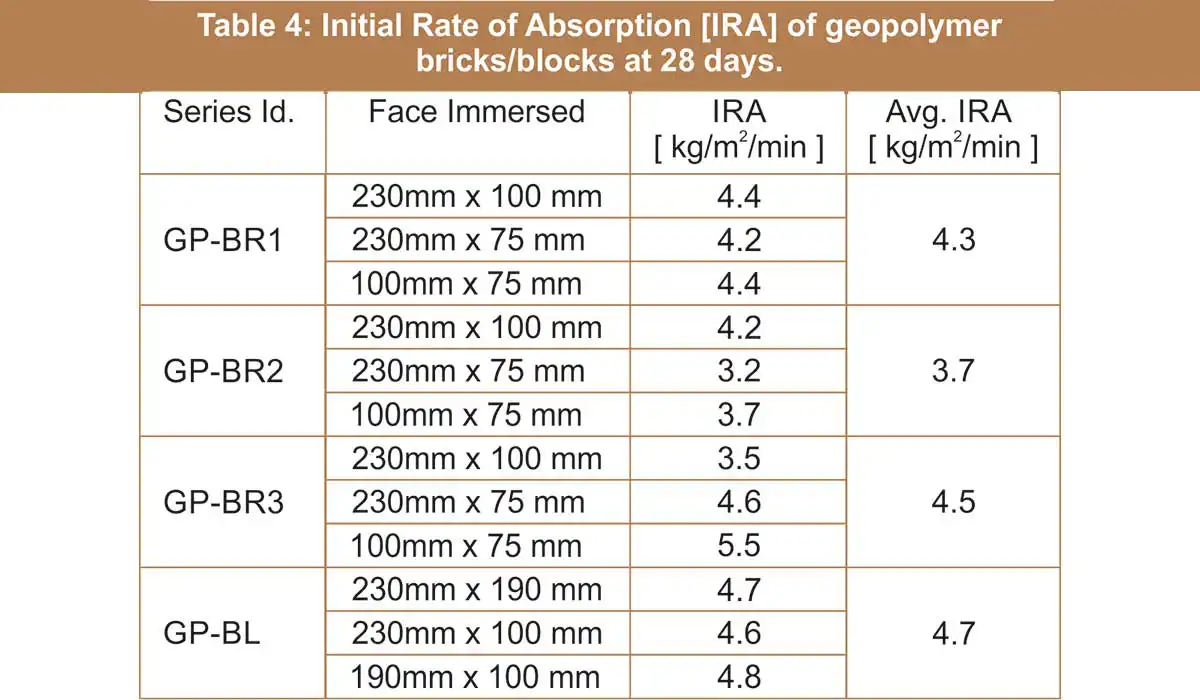
Materials and Methods
The following materials were used to prepare geopolymer masonry blocks/bricks:- Fly ash (Class F) and GGBFS,
- Manufactured sand (M-sand)
- Recycled water,
- Sodium hydroxide and
- Sodium silicate.
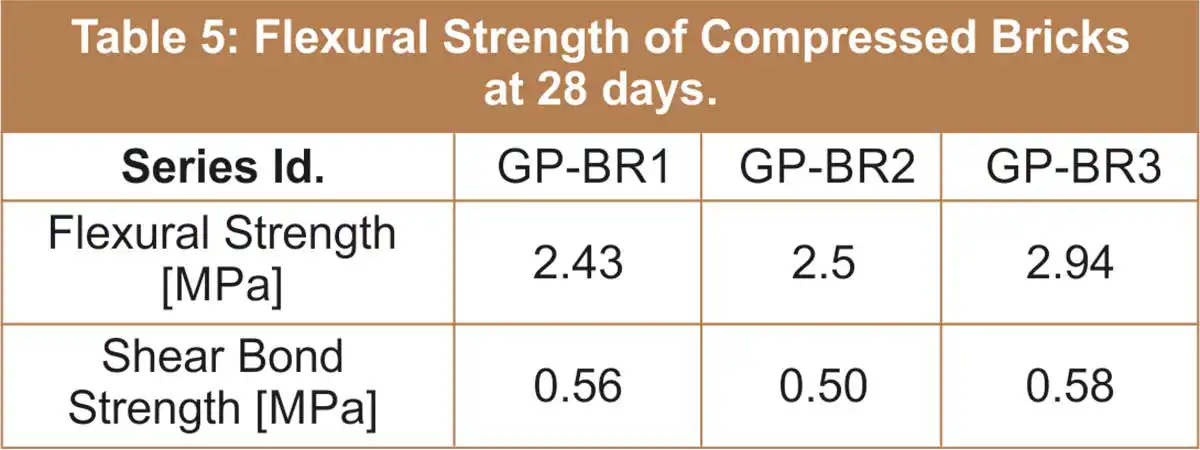
The fly ash, GGBSF and M-sand were first mixed thoroughly in dry condition and then alkali solution was added to prepare fresh mortar. The geopolymer block/bricks were prepared by compressing the required amount of mortar. The geopolymer bricks/blocks were cured in open air. The masonry units were tested for water absorption, initial rate of water absorption and density. The compressive and shear bond strengths were also determined along with modulus of elasticity.
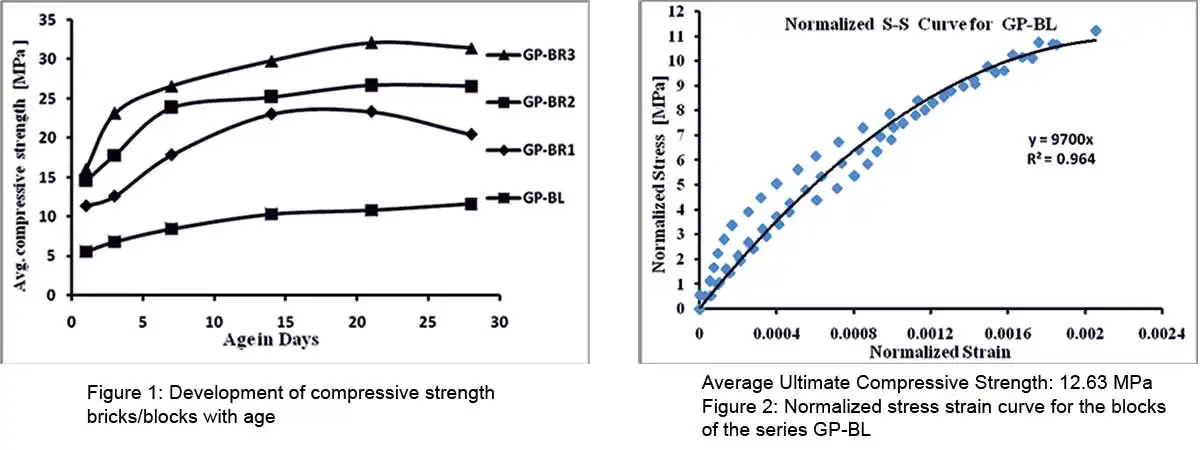
Results and Discussion
The water absorption and density of the bricks/blocks are tabulated in Table 3. It was found that the water absorption of the units rages from 8.7 to 9.6% which is considerably less compared to the traditional burnt bricks. The density of the units ranges from 1.87 to 1.98 g/cc which is par with the traditional units. Initial Rate of Absorption [IRA] of geopolymer bricks/blocks at 28 days are shown in Table 4 for various faces of immersion. IRA was found to be less than 5% which indicates that the masonry mortar will have god water retetntivity.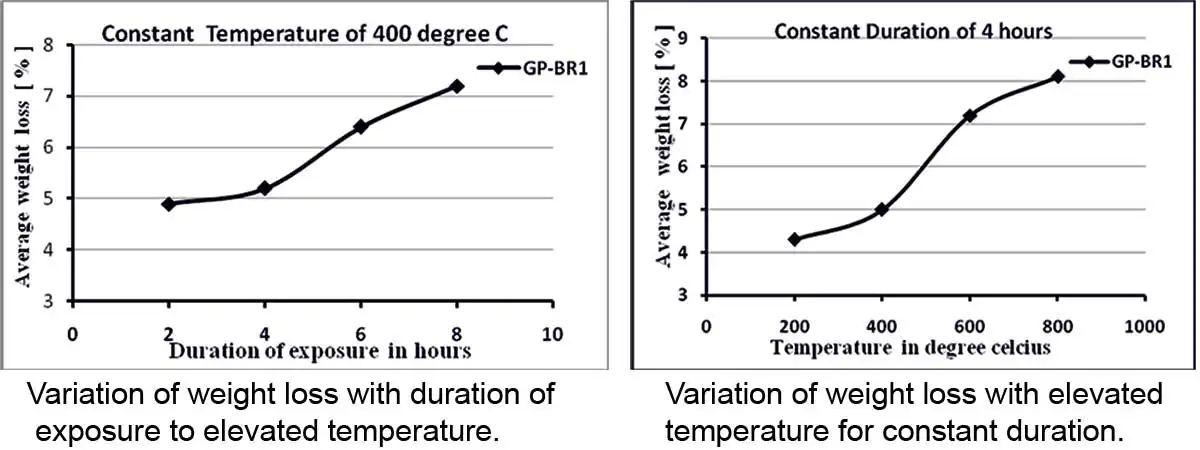
The variation of compressive strength of the units with age is indicated in Fig. 1. It can be observed that the compressive strength of the masonry units at the age of 24 hours is more than 5 MPa. This would be sufficient to handle the units for various purposes. The strength increases with age ranging from 5-32 MPa for the units.

The flexural and shear bond strength of the masonry units are very important properties. These propertiwes are shown in Table 5. It was found that flexural strength was more than 2 MPa nd shear bond strength is more than 0.5 MPa which is comparatively better than the traditional masonry.
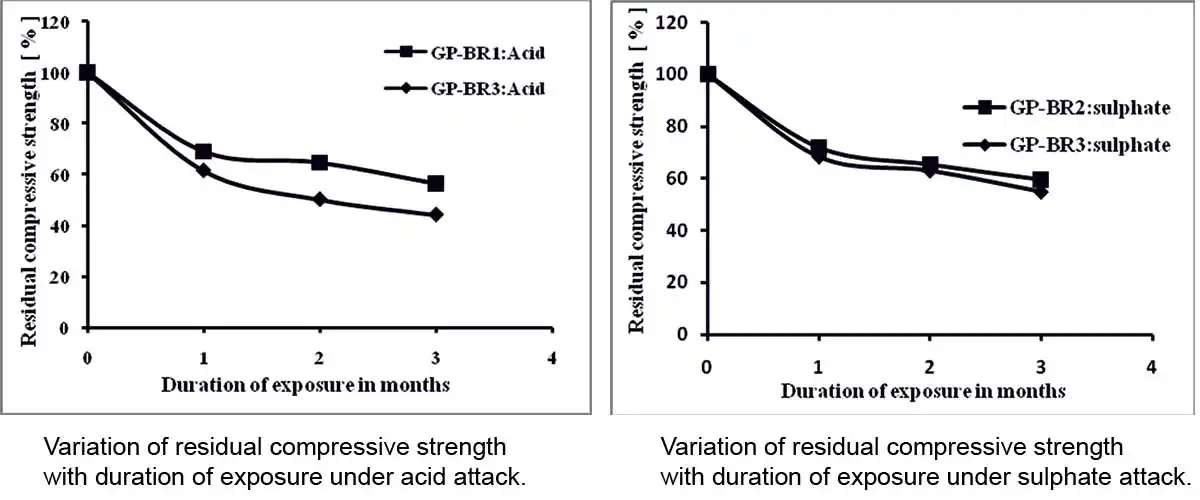
The variation of stress and strain was found be similar as that of traditional masonry unit as indicated in Fig.2 .The modulus of elasticity of geopolymer masonry block was found to be 9700MPa at the age of 28 days.
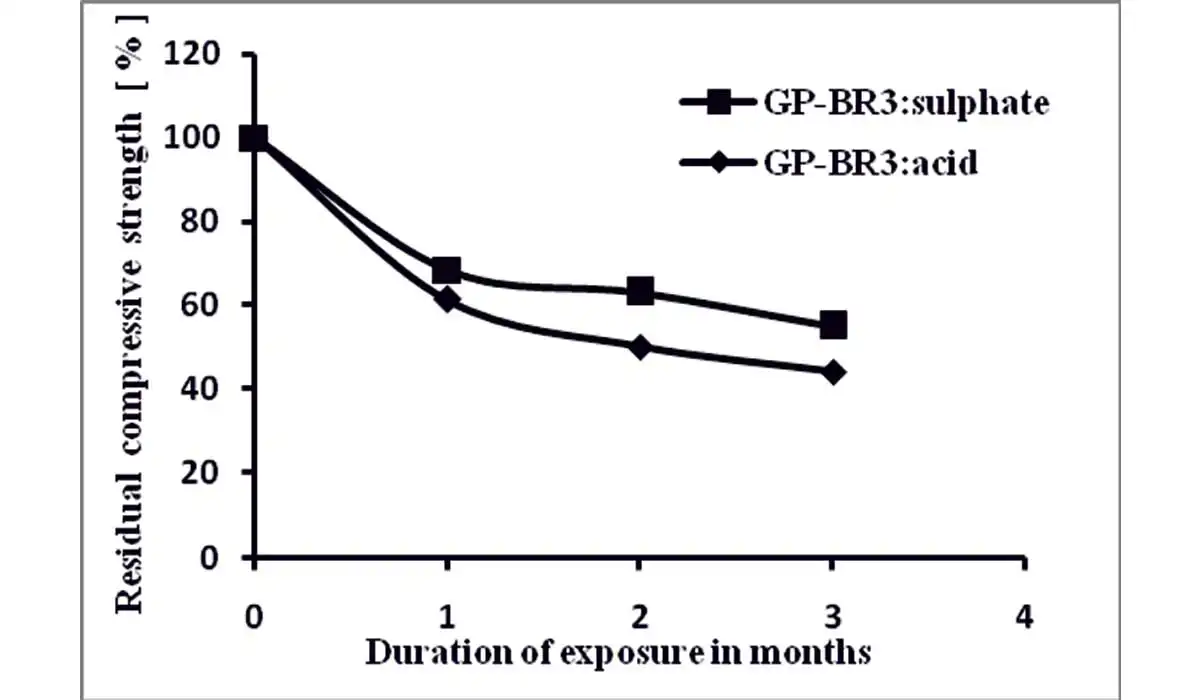
References
- Anita Fódi and István Bódi, Basics of reinforced masonry, Concrete structures, 3(1), 2011, pp 69-77
- Robert G. Drysdale and Ahmad A. Hamid, “Masonry structures behavior and design”, Third edition, Mcmaster University, Hamilton, Ontario, 2008
- Deepasree M Vijay., Poornima A Menon., Fathima Shahanas., “Environmental pollution from brick making operations and their effect on workers”, Biomarkers, 4(3), 2001, pp 162-166
- “Climate change and the cement industry” GCL-Environmental special issue, 2002.
- Joseph Davidovits, “Properties of geopolymer cements”, Proceedings of kiev state technical university conference, Ukraine, 1994, pp 131-149
- Andri Kusbiantoro, Muhd Fadhil Nuruddin b, Nasir Shafiq b and Sobia Anwar Qazi, “The effect of microwave incinerated rice husk ash on the compressive and bond strength of fly ash based geopolymer concrete”, Construction and Building Materials, 2012, 36, pp. 695–703.
- Rajamane N. P., Nataraja M. C. and Lakshmanan N., “Applicability of Acceptance Criteria of IS: 456-2000 to GGBS based Self Curing Geopolymer Concrete”, Proceedings of International Conference, Advances in Materials and Structures, ICI- AMAS-2011, Puducherry, India. pp. 370-378.
- Rajamane N. P., Nataraja M. C., Lakshmanan N. and Dattatreya J. K., “Pull-Out Tests for Strengths of Geopolymer Concretes”, Proceedings of International Conference, Advances in Materials and Structures, ICI- AMAS-2011, Puducherry, India. pp. 350-358.
- R. Anuradha, V. Sreevidya, R. Venkatasubramani and B. V. Rangan, “Relationship between Compressive and Splitting Tensile Strength of Geopolymer Concrete”, The Indian Concrete Journal, November 2011, pp. 18-23.
- K. Vijai, R. Kumutha and B. G. Vishnuram, “Experimental Investigation on Mechanical Properties of Geopolymer Concrete Composites”, Asian Journal of Civil Engineering (Building and Housing), 2012, Vol. 13, No. 1, pp. 89-96.
- Prabir K. Sarker, Rashedul Haque and Karamchand V. Ramgolam, “Fracture behaviour of heat cured fly ash based geopolymer concrete,”, Materials and Design, 2013, 44, pp. 580–586.
- Benny Joseph and George Mathew, “Influence of aggregate content on the behavior of fly ash based geopolymer concrete”, Scientia Iranica Transactions A: Civil Engineering, 2012, doi:10.1016/j.scient.2012.07.006.
- Saeed Ahmari, Xin Ren, Vahab Toufigh and Lianyang Zhang, “Production of geopolymeric binder from blended waste concrete powder and fly ash”, Construction and Building Materials, 2012, 35 pp. 718–729.
- Ali Nazari, “Compressive strength of geopolymers produced by ordinary Portland cement: Application of genetic programming for design”, Materials and Design, 2013, 43, pp. 356–366.
- Radhakrishna, Shashishankar A., Udayashankar.B.C and Renuka Devi. M.V., “Compressive Strength Assessment of Geopolymer Composites by a Phenomenological Model”, Journal of Reinforced Plastics and Composites, 4 Vol. 29, No. 6/2010 pp 840-852.doi:10.1177/0731684408100703 (Available online)
- Radhakrishna, “A Phenomenological Model To Re-Proportion Geopolymer Compressed Blocks”, Concrete Technology Today, Oct, 2008, vol7 No. 3 pp.46-48.
- Radhakrishna, Renuka Devi. M.V. and Udayashankar.B.C. “Use of fly ash in Construction Industry for sustainable development” Journal of Environmental Research and Development, volume 03, 2009, pp1211-1221.
- Radhakrishna, Shashishankar A. and Udayashankar.B.C “Analysis and Assessment of Strength Development in Class F Fly Ash Based Compressed Geopolymer Blocks” Indian Concrete Journal, Aug 2008, Vol 82, No.8.pp.31-37.
- Radhakrishna, Shashishankar A. and Udayashankar. B. C., Phenomenological Models to Proportion Geopolymer Compressed Blocks. Proceedings of The 33rd Conference on Our World in Concrete and Structures, Aug 2008, Singapore.
- Radhakrishna, Manjunath GS., C Giridhar and Mahesh Jadav “Strength Development in Geopolymer pastes and Mortars”, International Journal of Earth Sciences, ISSN 0974-5904, Volume 04, No 06 SPL, October 2011, pp. 830-834.
- S.M Tamizi, A.M Mustafa al Bakri, H. Kamarudin, C.M Ruzaidi, J Liyana, And A.K. Aeslina “Potential of Marine Clay as Raw Material in Geopolymer Composite”, Advanced Material Research, Vol626 (2013) pp963-966
- P.M. Vijaysankar, R. Anuradha, V. Sreevidya, Dr. R. Venkatasubramani “Durability Studies of Geopolymer Concrete Solid Blocks”. International journal of Advanced Scientific and Technical Research, ISSN 2249-9954, Issue 3 Volume 2, march-April 2013
- Sergio Tamburini, Monica Favaro, Andrea Magro, Enrico Garbin, Matteo Panizza, Fabiola Nardon, Maria Rosa Valluzzi. “Geopolymers as Strengthening materials for Built Heritage”, Built Heritage 2013 Monitoring Conservation Management.
- Paki Turgut “Manufacturing of Building bricks without Portland Cement” Journal of Cleaner Production 37 (2012) 361-367
- Breet Tempest Tara Cavalline, Jonos Gergely and David Weggel, “Construction and Demolition Waste Used as Recycled Aggregates in Concrete” Building Materials Reclamation Program - UNC Charlotte
- H.M. Khater, B.A. El-Sabbagh, M. Fanny, M.Ezzat, M. Lottfy and A.M. El Nagar “Effects of Nano-Clay on Alkali Activated Water-cooled Slag Geopolymer” British Journal of Science & Technology, 3(4): 764-776, 2013
- Susan A. Bernal, ruby Mejia de Gutierrez, Erich D. Rodriguez, “Alkali-activated materials: Cementing a sustainable future” Materials Engineering volume 15 no-2, p-211-223 (2013)
- John L. Provis “Geopolymers and other alkali activated materials: why, how and what?” Materials and Structures (2014) 47:11-25 DOI10.1617/s11527-013-0211-5
- Joseph Robert Yost, Aleksandra Radlinska, Stephen Ernst Michael Salera, “Structural behavior of alkali activated flyash concrete” Material and Structures (2013) 46:435-447 DOI 10.1617/s11527-012-9919-x
- Denis A. Brosnan “Characterization and Degradation of Masonry Mortar in Historic Brick Structures”, Hindawi publishing Corporation, Journal of Structures, volume 2014, Article ID 859879, 7 pages, DOI.org/10.1155/2014/859879
- Ronaldo S. GALLARDO, Mary ann. Q. ADAJAR “Structural Performance of concrete with paper sludge as fine aggregates partial replacement enhanced with admixtures” Symposium on Infrastructure Development and the environment 2006, 7-8 December 2006
- Andrew M Dunster “Characterisation of Mineral wastes, Resources and Processing Technologies-Integrated Waste management for the production of construction material- Case study on Paper Sludge ash in portland cement manufacture, WRT 177 / WR0115, October-2007.
ICCT - September - October 2023